成型是塑料镜头制造中重要的一步,成型件的精度一部分取决于产品形状设计和模具,另一部分取决于成型过程中的参数调节和成型后的精密检测。在塑胶镜头系列文章的第二章:材料中,已经介绍了多种热塑型塑料材料,这些材料的性质以及它们的来料形式(以塑料颗粒的形式入料进入成型机)。第三章中我们重点介绍了模具,塑料熔融材料流入模具型腔冷却后形成我们想要的形状。本章中我们会重点介绍注塑成型设备,注塑成型的流程,参数,以及它们对最终成型件(精品)的影响,成型后镜片的检测等内容。
注塑成型机历史,种类及厂家
历史
第一款人造塑料是由亚历山大·帕克斯(Alexander Parkes)于1855年发明的,他称这个塑料帕克西林(Parkesine)。1868年,美国发明家John Wesley Hyatt发明了一种使用注塑赛璐珞制造台球的方法(替代以前使用象牙制造台球的方法),1872年他和他的哥哥Isaiah Hyatt正式申请了该种方法的注塑机专利。最初的注塑机还非常原始,类似于大号的针管,但是已经可以很好的实现设计功能了。这个注塑机包括了一个柱塞(F),通过一个加热的圆柱(B),把塑料注入最下面的模具。
1946年美国James Hendry设计建造了第一款螺杆式注塑机,使用一个置于圆柱空腔内的螺杆,通过旋转把塑料材料前推和注入模具。旋转的螺杆提供了非常好的注入速度控制,可以进行材料混色等。今天95%的注塑成型机都是使用这种技术。
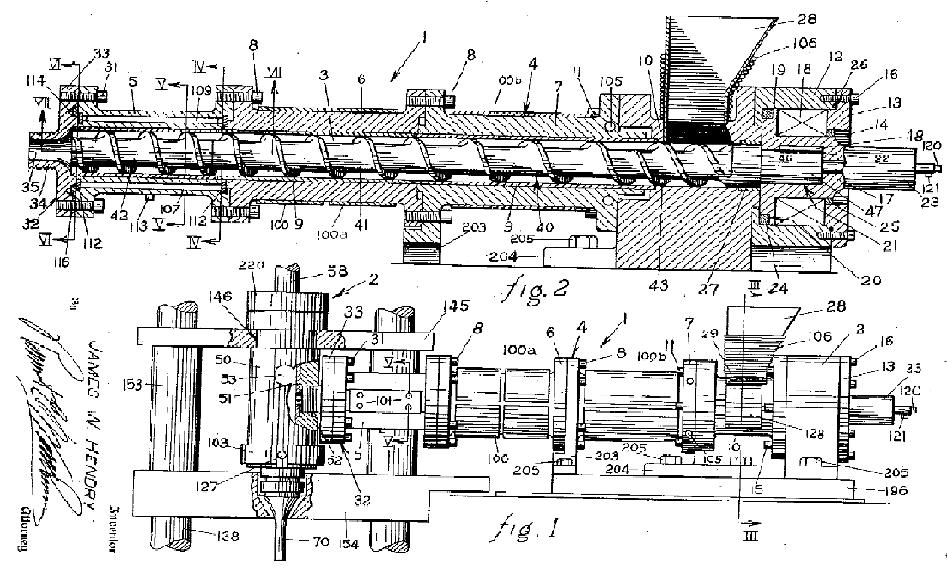
1956年W. H. Willert进一步优化了螺杆式注塑机,增加了往复挤出系统,在注塑成型的的阶段,熔融的塑料通过螺杆逐渐融化,被送入最前端,然后整个螺杆向前推送,把最前端的塑料注塑模具,然后后退,再把新一批熔融塑料送入前端。
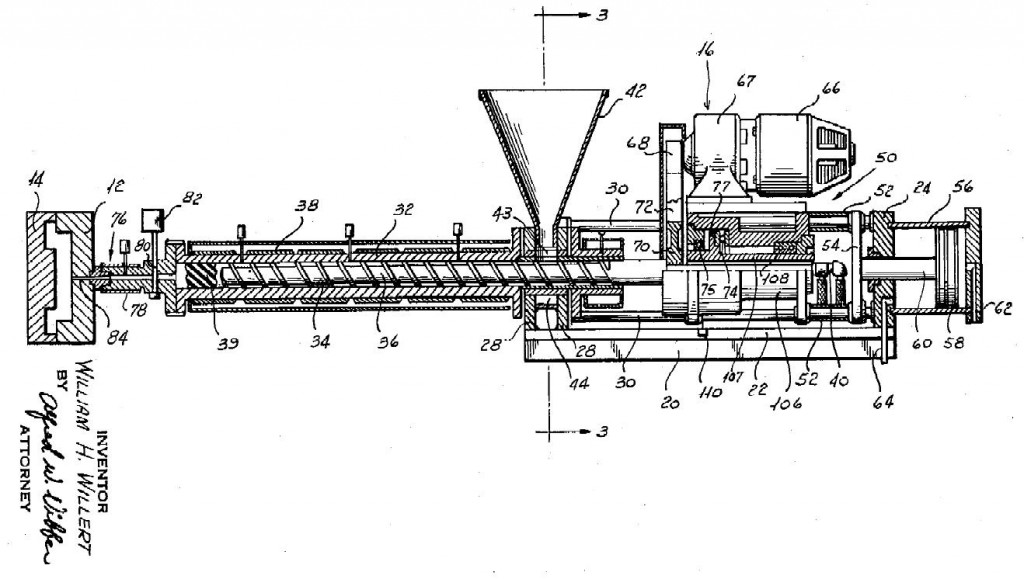
种类
按螺杆运动轴线和模板运动轴线相对位置分类,注塑成型机有卧式成型机(Horizontal),立式成型机(Vertical),角式成型机。
螺杆运动轴线和模板运动轴线在水平方向的是卧式成型机,在垂直方向的是立式成型机,螺杆运动轴线和模板运动轴线垂直的是角式成型机。三种成型机各有优劣,要根据生产产品的不同进行选择。
卧式成型机:成型机高度不高,厂房高度要求低,填料容易,但是占地空间大。模具横向移动,开模后产品直接掉落,需要机械手辅助取出。
立式成型机:高度高,填料麻烦,占地小。模具纵向移动,容易保持各个模穴的均一性。
角式成型机:优缺点介于立式与卧式之间。
厂家
用于手机镜头光学注塑成型的设备厂家主要有:
Sumitomo (SHI) Demag塑料机械有限公司是全球最大的塑料加工注塑机制造商之一。这家日本—德国公司于2008年春季成立,合并了住友重工(SHI)和德马格塑料集团的注塑成型业务。Sumitomo (SHI) Demag在全球的开发和生产网络包括日本,德国和中国的四家工厂,员工人数超过3000人。该产品组合包括全电动,液压和混合注塑机,锁模力在180和15,000 kN之间。住友(SHI)德马格在全球所有重要市场均设有超过100,000台机器。每年售出超过5000台机器,Sumitomo (SHI) Demag的塑料机械业务已成为全球最大的注塑机制造商之一。
Fanuc发那科,是一间提供如机器人和电脑数控机床等自动化产品服务的公司,主要由日本“发那科公司”(日语:ファナック株式会社 Fanakku Kabushikigaisha)、美国密歇根州罗切斯特山的“美国发那科公司”以及卢森堡的“欧洲发那科公司”组成。 发那科是世界上最大的工业机器人制造商之一,公司名称是富士自动化数控(Fuji Automatic Numerical Control)的英文缩写。最早期的发那科公司是富士通开发的早期数字控制和伺服系统公司的一部分。
考虑到手机光学镜片注塑成型需要的锁模力相对较小,一般使用的都是30T或者50T的机型。
注塑成型机结构
前文我们讨论了注塑成型机的历史,了解了注塑成型机的主要结构,在这一节中我们在具体讨论这些结构,参数以及注塑成型机的参数对于光学产品的影响。下图展示了一台卧式注塑成型机的结构,蓝色上部右侧是最注塑结构,主要包括料筒,螺杆等,蓝色上部左侧是模具和锁模机构位置,模具的固定侧固定在靠右侧的螺杆处,左侧的锁模机构带动模具可动侧进行模具的开合。整个注塑成型机的下部是控制设备和承台等结构。
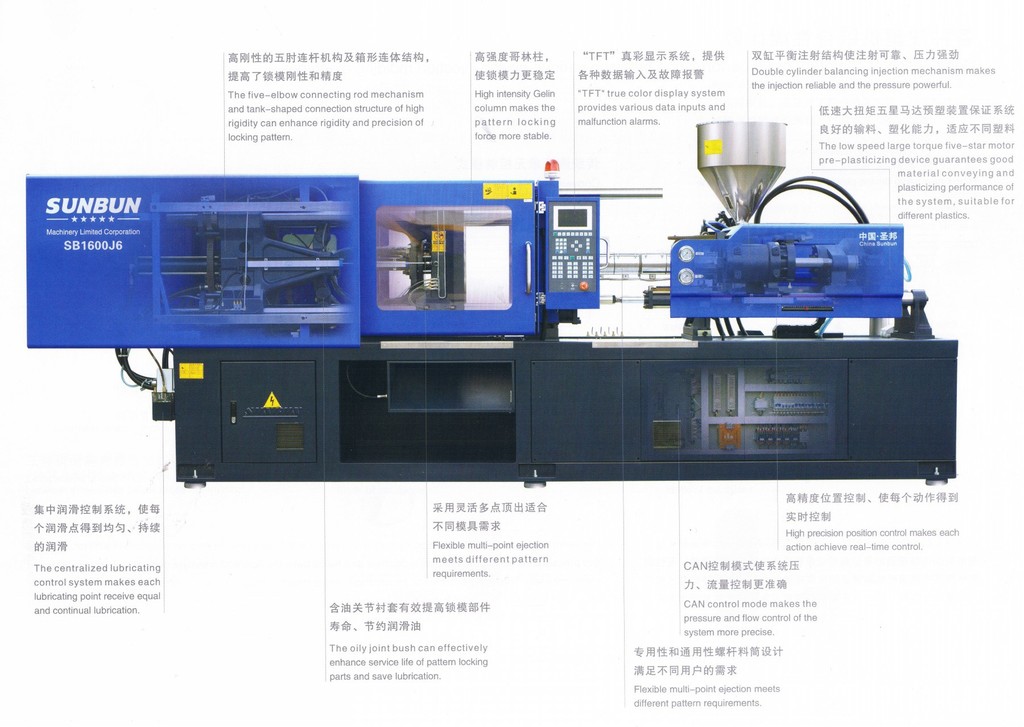
注塑成型流程
Polyplastic这张动图,很好展示了注塑成型机的流程和螺杆的结构。基本流程包括原料处理,合模,注塑,V/P转换,保压,冷却,开模,顶出,制品取出,我们在下面详细讨论这些流程。
塑料原材料干燥
塑料原材料是需要干燥后才能进入注塑流程的,如下图Zeonex的说明所列,需要通过预先干燥4-10小时去除溶解的空气中的水分以防止成品颜色灰暗,产生碳化物及空隙。
注塑氮气保护
进行注塑成型的时候,要进行氮气保护以防止出现碳化,烧焦,变色等情况。
合模
模具闭合,模具的可动侧由注塑机带动和固定侧锁闭。注塑成型机的锁闭机构,控制机构,模具机座结构都会对塑胶镜片的制造精度产生影响。
注射,V/P转换及保压
料筒中的塑料颗粒进入螺杆,螺杆旋转把所料颗粒前送,随着塑料颗粒经过加热段,逐渐变成熔融态,被推入最前射出段,整个螺杆前送,推送最前端的塑料进入模具(此时料筒停止供料),而后螺杆后退,螺杆旋转准备再次送料。这个步骤看起来简单,但是其实包含了几个分解步骤,而且也是成型参数中最重要的部分。其中有注射阶段,V/P转换阶段和保压阶段。一般使用压力,速度曲线来描述这一过程。同时,成型机上对于不同的步骤都可以进行分别的设置。
注射
注射过程指的是螺杆前推把熔融塑料推入模具的过程,该过程不是以一个固定速度进行的,而是分几个步骤,在不同阶段使用不同的注射速度完成对模具型腔的填充。比如对于一台五速四段成型机,在注射设置中,就会有五个匀速运动状态。见上图绿色曲线的前五个定值,就是螺杆前进的五个速度。对于小型塑料镜片注塑来说,首先第一个速度是熔融塑料快速被推入主流道,第二个速度是塑料到达主流道末端开始进入分流道,第三个最低速度是塑料通过浇口(防止出现喷射纹以及浇口雾斑等现象),然后进行一个高速注入(以减小腔内熔料温差,改善压力传递效果,得到密度均匀,内应力小的镜片,提高熔接缝强度等作用)。这部分对应的压力曲线可以看到是一直上升的。最后的低速是V/P切换后的速度。这里的设置主要有螺杆4个位置的设置,和到每个位置螺杆运动的速度(共5个)。
V/P转换(Velocity/Pressure Switch)
前面的注塑流程上主要负责把塑料注入模具型腔,填充满。在这个过程中,螺杆的运动主要是通过控制前进速度来完成,当模具型腔快要填满时,就需要开始控制型腔内塑料的压力,要防止压力太大造成飞边,内应力过高等问题。这时,螺杆的运动就由流动速率控制转换到压力控制,这个转化点被称为保压切换控制点,既V/P转换点。切换方式一般有三种,为压力切换,时间切换和位置切换。压力切换就是当机器检测到射出压力达到设定压力时,转换为压力传感器控制螺杆运动;位置切换为当螺杆运动到某一设定位置时,转换为压力控制传感器控制螺杆运动;时间切换为当注射开始一段特定的时间后,转换为压力控制传感器控制螺杆运动。
保压
V/P转换后,螺杆会通过继续前移,填充满模具并达到一个设定的保压压力。保压压力也会有几个阶段,可以从曲线看到,这里保压压力有三个阶段,随着成型件冷却固化,逐渐降低保压压力。
冷却
产品在模具中冷却,直至达到设计的冷却时间。冷却时间是决定注塑生产效率的重要参数。
开模,制品顶出及取出
模具打开,制品被顶出,然后被机械臂取出。模具合模进行下一次注塑。
剪切
被机械臂取出的多穴镜片会放置在剪切机上,由热刀和流道分离,并自动化装盘。
烘烤
镜片剪切装入镜片托盘后,为了进一步降低内应力,优化镜片的性能(MTF及信赖性),会进行烘烤。烘烤的实现主要是把镜片放置入特定温度的烤箱中一定时间自然冷却或者控制温度逐渐降低退火。比如放置入75℃-95℃的烤箱中3-5小时,然后自然冷却。
模流分析
注射成型过程会影响光学零部件表面面形精度,由于材料在成型过程中的流动模式和冷却,固化收缩,光学零件的面形精度会受到影响。现代塑料成型的模具和成型参数设计都先使用计算机辅助设计来进行模流分析,如Autodesk Moldflow Adavisor,Autodesk MoldFlow Plastics Insight (MPI),Moldex3D等。这些软件可以通过3D建模,然后输入成型注塑的速度温度等参数,然后分析塑料在模具内流动情况,填充情况(填充度,熔接痕),填充压力,填充时间,冷却时间,压力变化,锁模力需求,模具困气等。实际开发中,会在仿真中先一步优化成型产品的形状控制,应力分布,折射率分布,优化成型时间,直到模流分析显示出较好的结果,然后镜片的设计优化确认后,模具的生产才会开始,这样可以避免后面对模具进行重新设计或进行大的修改。
下面的动图展示了常见的模流分析软件进行分析后生成的动图,在这个看起来像是注塑乐高拼图的模流分析中,用户可以看到塑料在模具中的流动状况,在这个图里,还可以看到颜色代表的温度的动态变化。
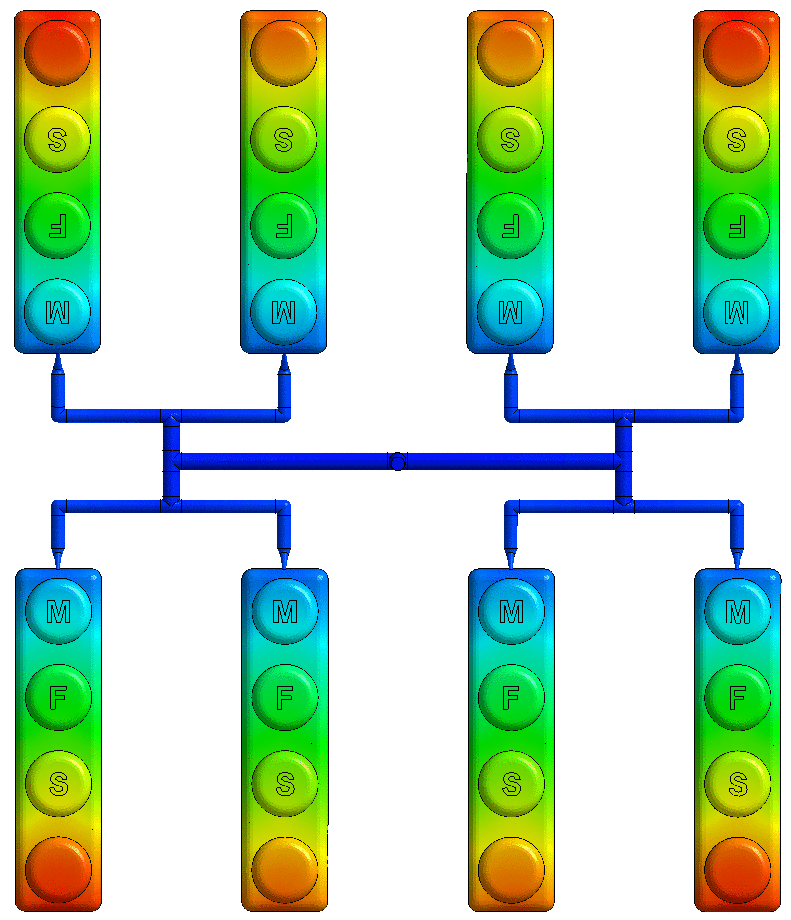
对于光学部品,主要要分析的是形状(尺寸相关参数)以及外观,模流分析主要针对以下几点进行分析,这里主要对需要注意的问题进行简单介绍,注塑成型的具体细节可以咨询成型工程师。以下以镜片成型为例子,镜筒成型考虑的问题类似:
- 以下所有参数在不同模穴的分布情况(有一些流道设计可以多模穴很均匀,有些则不然)
- 填充是否饱满:这决定了产品形状
- 面型:影响成像质量
- 熔接痕:熔接痕是熔融塑料交汇的位置,对于有些形状的镜片,如下图所示Link,展示了两种成型条件下的模流分析和熔接痕情况。左边的一组显示注入的塑料可能分成两路最终在浇口对侧汇聚,这时可能会形成熔接痕,而右边的是优化过后的成型状态。熔接痕的长度和位置都很重要,如果在镜片的有效径内,影响光学性能,造成杂光;在有效径外也可能造成杂光或者影响组装精度,不好的熔接痕也可能造成信赖性后的镜片开裂。
- 飞边:飞边产生于模具的两侧接缝处,如果此处闭合不严,或者模具打开时模具内压力还比较高,或者锁模力不足都可能造成一些塑料溢出形成飞边。飞边会影响塑料镜片的外周精度,影响组装;同时飞边可能非常小,在微米级别,可能会掉落污染镜头或者产线,造成外观不良。
- 困气:因为模具闭合很严,当塑料注入时,模具内的剩余气体被压缩,可能在塑料最终到达的位置无法排出,造成困气,进而造成填充不满。解决困气需要设置模具排气或者抽真空。
- 气泡 :许多工艺参数对产生气泡及真空泡都有直接的影响。如果注射压力太低,注射速度太快,注射时间和周期太短,加料量过多或过少,保压不足,冷却不均匀或冷却不足,以及料温及模温控制不当,都会引起塑件内产生气泡。高速注射时,模具内的气体来不及排出,导致熔料内残留气体太多,如果速度降得太多,注射压力太低,则难以将熔料内的气体排尽,也很容易产生气泡以及凹陷和填充不均匀。Link
- 白斑,流痕:温度不够,压力不够可能会产生白斑;射速太高可能会产生流痕问题。
- 应力分布:见下图左,Moldex3D模流分析可以展示出应力的分布。应力会造成应力双折射,影响光学性能,也会造成可能的信赖性问题(开裂等)。
- 折射率分布:见下图中,Moldex3D模流分析可以展示出成型后的折射率的分布。
- 翘曲:见下图右,Moldex3D模流分析可以展示出镜片的翘曲情况。
成型品的最终状态由产品设计(产品形状),模具设计(流道,浇口大小及形状,排气,加热/冷却设计,顶出)和成型参数(前文注塑成型流程中所述参数)共同决定。我们会在最后一章,设计中再次列出这里所有需要考虑的参数。
成型后的检测
成型后剪切下来的镜片会进行各种参数的测定,其中包括面型,偏心,应力双折射,透过率,外观等。
面型检测
精确的面型检测对于现在手机镜头镜片尤其重要,现在手机镜头厂的标准配置设备是Panasonic UA3P轮廓仪。该系列设备使用原子扫描方法,可以达到非常高的面型和偏心测量精度。比如标准设备UA3P-300在最大30°的表面轮廓下,30mm x 30mm x 20mm的范围内,往复测量精度为±0.05um。同时UA3P提供了很多配套软件进行面型的分析。
读者如果感兴趣,可以阅读设备的简介,UA3P系列英文介绍
偏心检测
偏心检测主要检测镜片的面间偏心,常用的设备有UA3P和Trioptics OptiCentric系列。如今的手机镜头镜片偏心值非常小(1um~2um),需要设备精度和设备间均一性很好。使用UA3P进行偏心测量,是通过测量镜片机械重心和光学重心,确认偏心值。使用Trioptics是把镜片放置到治具上进行旋转测定。两种方法各有优劣,比如UA3P可以进行编程对一个托盘的镜片进行面型和偏心测量,不需要单个镜片人工测试。
中厚检测
镜片的厚度是重要的光学参数,可以使用激光测厚仪来进行测量。比如Trioptics的OptiSurf,厚度测量精度可以达到1um。
应力双折射检测
多种设备可以进行应力双折射的检测,如Photonic Lattice的WPA系列,Thorlabs的LCC7201等。
透过率检测
透过率检测主要是确认成型后镜片达到该种材料的成型后透过率标准,发现人眼无法发现的透过率损失。
外观检测
外观检测主要检测成型品是否有熔接痕,白点/黑点,雾面,杂质,困气,飞边等等外观问题。外观检测主要通过肉眼及显微镜等设备进行。
镜筒的检测
镜筒的检测主要是尺寸检测和外观检测,尺寸检测主要使用各种三坐标设备,外观检测主要使用显微镜等设备。
成型车间的生产流程
实际生产中,首先的设计阶段会进行镜头镜片结构设计,模具设计和模流分析,然后进行多轮设计优化。产品定型后,开始模具加工,模具加工完成后,会进行单穴,双穴或者四穴成型调试,然后会进行测量,测量数据返回设计部门进行公差分析,再进行进一步调试达到设计公差范围内。都达到标准后,模具扩穴(开始使用所有模穴),进一步进行调试,直到参数稳定,最终开始进行大规模生产。生产中的成型参数可能也需要进行微调。一个光学镜头制造工厂的成型部门接受的输入是镜片设计和公差要求,输出的是为下游提供合格的单镜片零件。
版权声明: 感谢您的阅读,本文由超光版权所有。如若转载,请注明出处。