在前面几章我们已经了解了镜头中各个零部件制造的关键步骤和参数,下一步就需要把各个零部件组装在一起,这就是镜头组装。镜筒组装的最终目的是完成整个镜头的制造,实现光学性能,同时达到该镜头需要的外观及信赖性要求。前面几章介绍的材料,模具,注塑成型,镀膜和其中包含的各种检测工序都是为了最大程度的实现部品的高精度和部品之间高均一性,但是,部品依然是不完美的,存在一定公差。在镜头组装的环节,这些公差会相互作用,降低镜头光学品质和信赖性。通过在镜头组装阶段采用各种方法控制这些公差,最终可以实现高品质,高良率的镜头。
镜头组装流程及设备
讨论公差控制前,我们先简单介绍组装的基本流程和设备。镜头组装的基本零部件是镜筒,镜片,隔片和隔圈。镜筒承担着整体支架的作用,用于承载所有其他零部件。由于体积限制,制造工序的优化需求,手机塑料镜头的组装相对比较简单,基本都是从一个方向把所有零部件按顺序放入镜筒。如下图所示,镜筒前端朝下平放,镜片,隔圈,隔片,压圈等被按顺序组装进入镜筒,然后点胶固定。根据镜头具体设计不同,也会有从镜头前端组装,或者从镜头两侧分别组装的方式(先组装完一侧,然后镜筒翻转,从另一侧继续组装。该视频是韩国KIT公司展示镜筒组装设备的视频,其中展示了零部件组装和点胶固定的流程。
镜筒排盘
组装的第一个步骤是进行镜筒排盘,既把镜筒排布在组装托盘中。镜筒生产出来后的传送托盘一般为塑料托盘,主要用于转运镜筒,精度较低,不适合用于组装,组装时需要把镜筒放置入高精度组装托盘中。组装托盘一般会采用精密加工的方式进行加工,以达到高度的平整度以及光洁度。用以保证组装精度及镜筒表面光洁度。
镜片组装
镜片,隔圈,隔片,压圈组装都是由自动化完成,主要流程为排盘->图像识别->吸取->图像识别->旋转/移动->组装。
1)首先这些零部件也会经过排盘,镜片会由简易的塑料传送托盘中被转移到组装托盘中,用以保证被吸取时的平行度。隔圈,隔片,压圈会被确认朝向后,放置入组装托盘中等待被吸取。
2)图像识别系统会定位待组装镜筒的位置和旋转角度,镜片/隔圈/隔片/压圈的位置和旋转角度
3)识别后,由吸嘴移动到镜片/隔圈/隔片/压圈上方吸取零件
4)吸嘴再次移动到一个图像识别照相机上方,确认零件在吸嘴的位置和角度然后根据设定,把零件相对于镜筒的角度进行一定旋转(为什么要进行旋转我们在后面良率控制会进行解释)并移动到镜筒上方
5)吸嘴下压组装进镜筒。
这个过程中精度控制十分重要,同时有一些设备也会有同心度检测,如果发现组装偏移,下一个部件的组装就会略过这个镜头,不再进行下一个阶段的组装。
固定
最后的压圈组装完成后,会进行整体的固定工序。这一步的实现方式主要是通过点胶。胶水的种类主要有UV胶(点胶完成后使用UV光照射固化),热固胶(通过提高温度固化),双固化胶水(点胶完成后先进行UV照射,部分固化,再通过烘烤提高温度,彻底固化,优点是在刚组装好后就可以进行部分固化,避免了移动带来的镜片位置变化,同时又通过热固定实现了最终的高牢固度)等。
设备
整体设备分为流水线式组装机和一体式组装机。
流水线式组装线:是流水线形式的设备,每一个单台设备实现一个或者两个单一步骤,比如第一台机器负责镜筒排盘,第二台机器负责组装镜片1到镜筒,第三台机器负责组装隔片1到镜筒,以此类推,最后一台机器负责点胶固定。流水线式的组装UPH(UPH,unit per hour)较高,每台机器各司其职,单独开发调试。但是流水线式的组装设备,组装托盘由操作员在各设备中进行移动或者是在设备中通过传送带或者传送机构进行传送,这个过程中会产生可能的震动,造成镜片位移,造成镜头组装品质下降,所以要特别控制传送中产生的震动。下面两张图示韩国KIT公司生产的组装产线,可以看到每一台机器都可以组装一个镜片加一个隔圈/隔片/压圈,以此类推。下面展示的两种设备的区别很小,第一张图是人工进行镜头在设备到设备间的传送,第二张图是完全自动化从第一台机器一直传送到最后一台机器。
一体式组装机:一台设备形式,所有物料在一台机器内,这台机器包含了镜筒排盘,零件组装和固定所有工序。优点是非常适合试做阶段,同时由于镜筒托盘进入机器后不会再次移动,不会产生由于镜筒托盘移动产生的位移,组装时设备稳定性好。缺点是一体式组装UPH较低,同时组装的吸嘴为了配合不同物料可能有多个,成一列分布。
组装设备相关参考公司网页:韩国Zeroneco,鸿辅科技,AKIM等
MTF良率控制
手机镜头组装后要进行光学性能检测,外观检测和信赖性测试,通过这些检测的镜头才能出货,未通过的镜头为不良品,会被废弃。手机镜头整个生产流程上有多道良率分析,成型良率,镀膜良率,组装后镜头光学性能良率,组装后镜头外观良率等。这里我们主要讨论组装后光学性能良率控制,或者称为MTF良率。
良率控制的关键是了解公差,公差控制/补偿以及检测手段,既了解当前零部件有哪些公差,这些公差是如何分布的,是如何作用到光学性能上的,有哪些手段可以控制,调整,补偿以及检测。
公差及对成像的影响
首先我们可以把公差分为两组,一组为零件本身的公差,一组为零件和零件相互作用可能产生的公差。这些公差都会降低光学性能。(我们在这里尝试较少讨论公差具体会如何影响光学性能,比如具体时间如何影响MTF等,更多的从如何做一个更接近设计图纸的镜头去思考这个问题)。
零件本身的公差:镜片中厚,镜片法兰厚度,镜片外径及圆度,镜片面间偏心,镜片面型,镜筒内径及圆度,隔圈厚度。这些公差的分布都是来源于零部件制造,模具到模具之间,模具的每个穴之间,公差的具体值不同。
零件之间的公差:镜片之间的组装偏心,镜片之间的倾斜,镜片之间的空气间隙,镜片外径到镜筒内径之间的距离。这些公差的最终分布取决于组装流程的参数控制。
偏心控制是塑料镜片生产中的最重要的课题之一。
公差控制及补偿
对于零件本身的公差,控制方式自然是尽量把零部件制造的符合设计,收窄分布。需要注意的是,公差永远无法完全消除,降低公差在逐渐接近极限的过程中,会极大地增加成本。
在本章,我们假设我们的零部件已经达到设计公差,此时这些零部件是不完美的,由于大部分是注塑成型零件,这些零部件模具和模具之间,穴与穴之间都是有轻微不同的。我们重点讨论如何通过零部件之间的搭配和镜片旋转搭配来实现最终的光学性能提升。对于如何通过设计,在设计阶段更好的实现后道制程的公差控制和公差分配,我们会在第八章再去讨论。
零部件搭配
我们首先用一个例子说明零部件搭配的概念,假设我们一批镜筒和镜片,他们都是是由两穴模具制造出来的。镜筒内径和镜片外径的设计值都是5mm,公差±2um。对于镜筒,1号穴的内径成型后稳定为4.999mm,2号穴的内径成型后稳定为5.002mm。对于镜片,1号穴的内径成型后稳定为5.001mm,2号穴的内径成型后稳定为4.998mm。可以看到,如果我们就是随意去组装的话,1号穴的镜片如果装入1号穴的镜筒,大一些的镜片对小一些的镜筒,镜片会产生较大应力,而如果2号穴的镜片装入2号穴的镜筒,小一些的镜片对大一些的镜筒可能在里面会有位移。但是如果1号穴的镜筒和2号穴的镜片组装,2号穴的镜筒和1号穴的镜片组装,那么两种的组合都可以实现很好的最终结果。
类似的例子有:
1)法兰厚度搭配,L1镜片法兰偏厚,可以用L2镜片法兰偏薄的和其配合组装,用以保证镜片间的空气间隙。
2)面型搭配,两个不完美的镜片面型可能搭配起来会被混装产生更好一些的光学性能。
3)镜片偏心搭配,来自于不同的穴的镜片,偏心值不同,偏心方向不同(相对于镜片浇口的方向)。对于镜片偏心搭配,要结合镜片旋转组装来实现更好的性能。
镜片旋转搭配组装
假设我们有一个2P的镜头,L1和L2都是由两穴模具生产出来的。
对于L1的镜片,来自于1号穴的镜片偏心为1um,光轴是偏向镜片料口方向,来自2号穴的镜片偏心为2um,光轴是偏向料口对侧方向。
对于L2的镜片,来自于1号穴的镜片偏心为1um,光轴是偏向镜片料口对侧方向,来自2号穴的镜片偏心为2um,光轴是偏向料口方向45°。
首先,要做的是穴的搭配,我们使用来自于1号穴的L1和来自于1号穴的L2进行组装,然后是旋转搭配。
如下图所示,紫色的是L1镜片,绿色的是L2镜片,其中镜片的机械重心是黑色圆点,镜片的光学中心是橙色圆点。对于L1-1和L2-1的组合,在组装时,L1会被旋转180°,和L2的光轴对准组装进镜片。对于L1-2和L2-2的组合,L1会被旋转135°,和L2的光轴对准组装进镜片。这样就保证了镜片的光轴是对准的。实际组装中,图像识别系统识别镜片的注塑料口确认镜片的旋转方向,然后组装吸嘴进行相应的设定角度旋转,再进行组装。
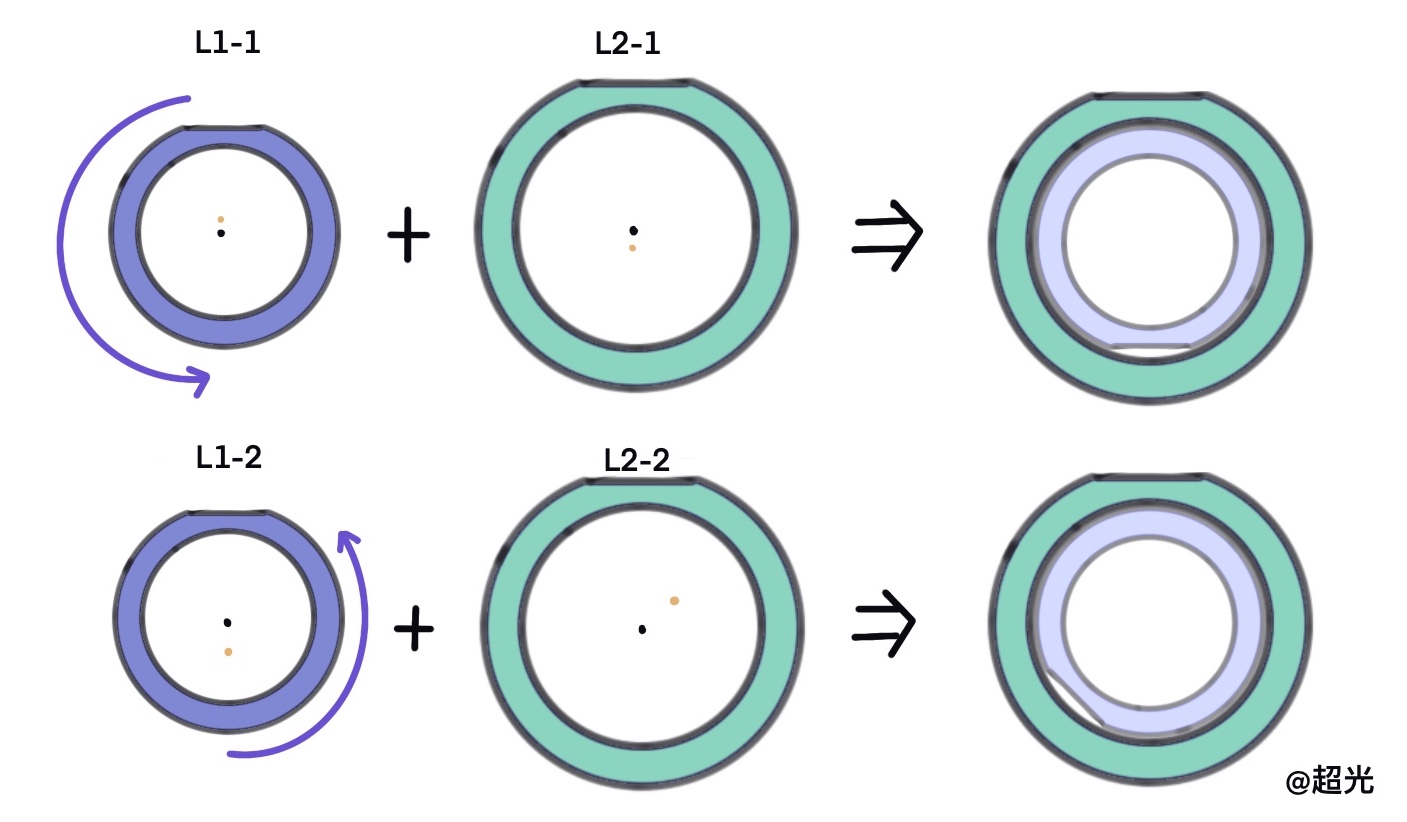
下图展示了未通过旋转组装的镜头的MTF离焦曲线和进行了旋转搭配组装后的MTF离焦曲线的区别。可以看到,不经过光轴对准组装的镜头在0视场MTF最高时,轴外视场MTF并未达到最高值,而是有各种偏移。通过光轴对准,可以消除这种影响。
旋转哪片或者哪几片镜片是要根据实际生产情况和公差分析决定。比如设计上,L6本身的偏心对镜头整体品质影响并不大,就可以不进行旋转。
在生产过程中,镜片的注塑成型会出现偏移,造成偏心的大小和角度发生变化,组装镜头品质下降,此时就需要根据镜头的检测结果,进行旋转角度的调整。
搭配的确认
现代大规模生产中,对于一个7P的镜头,可能会有很多套模具,模具上根据镜片大小不同,可能从16穴到32穴不等。如此,有非常多的组合方式。如何快速地找到合适的搭配,提高镜头良率,是一项非常重要的工作,每个公司有自己公司的方法论和方法流程。比如尽量把各个零件生产的很好,用所有的1号穴进行组合,只进行旋转搭配。寻找搭配是在有限的时间内,找到尽量多的可以稳定生产的搭配。对于镜头的良率,从30%提升到80%非常有必要,可能需要10位各部门的工程师一起工作1个月时间;但是从80%提升到85%,可能需要这10位工程师再一起工作1个月,那么考虑综合经济效益,这些工程师会被指派其他任务,镜头良率优化暂停。
组装过程中检测
有一些镜头的组装过程中也会进行偏心检测,对于照相机镜头等使用人工组装的镜头,组装中进行对心是非常常见的步骤,对于手机类镜头,由于需要达到很高的UPH,并不会进行动态的偏心检测和动态调整。这里的检测如图所示,主要是使用激光偏心测量的方式确认没有很大的偏心发生(比如镜片装倾斜),如果有很严重的组装倾斜发生,该镜筒就可以在后面的组装中被忽略不进行下一个镜片的组装,以节约成本。
镜头设计和组装
镜头的设计以及公差分析对于镜头的组装至关重要,设计是和组装流程互相影响的,这里我们举一个简单的例子进行说明,具体的设计讨论会在第八章进行。
对于镜头的结构设计,镜片如何组装在镜筒中有多种设计方式,其中有堆叠式,扣合式和混合式。堆叠式既镜片的法兰一片一片叠合在一起,镜片外径和镜筒内径接触,这种方式镜片间的偏心位置可能不好控制,镜片和镜筒之间可能有空洞。扣合式是用镜片和镜片的法兰结构进行配合接触,用一个镜片去保证另一个镜片的相对位置,优点是组装较低依赖镜筒内径精度,镜片的精度较高,可以很好地控制对准,但是如果镜片到镜片之间的距离过大,这种方式无法实现,还是需要使用隔圈等进行堆叠组装。
版权声明: 感谢您的阅读,本文由超光版权所有。如若转载,请注明出处。